Home » Posts tagged '3d printing design'
Tag Archives: 3d printing design
How 3D Printing Works
3D printing is a new type of manufacturing that builds parts layer by layer. It is used for rapid prototyping and mass production. Here’s how it works:
To begin with, a virtual design of the object is made. This is usually done using CAD software, a computer program that can create precise drawings and technical illustrations. Contact By3Design now!
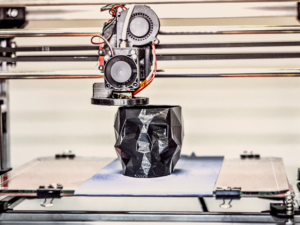
Additive manufacturing is a technology that uses a 3D printer to build objects by adding material rather than subtracting it. It is also called digital fabrication and is part of the Industry 4.0 suite of technologies, which includes data analytics, machine learning, AI, cloud computing, and automation.
It is a powerful tool that can reduce production time and improve energy productivity. It can also enable design flexibility and create high-impact jobs. This technology is one of the primary focus areas of the U.S. Department of Energy’s Advanced Manufacturing Office (AMO).
A 3D printing system transforms digital inputs into physical outputs by building layers of material, layer by layer, until the final object is completed. The finished product can be used for a variety of purposes, including prototyping, product design, and industrial applications. Additive manufacturing can create complex shapes and geometries that would be impossible or impractical to make using traditional methods. It can also be used to produce spare parts for existing equipment.
Currently, the most common method of additive manufacturing is fused deposition modeling, also known as FDM. This technique uses a heated nozzle to melt plastic filaments, such as PLA (Polylactic Acid), ABS (Acrylonitrile Butadiene Styrene), and TPU (Thermoplastic Polyurethane). These materials are then applied to a build platform in layers, one at a time. The process is extremely quick and inexpensive, making it an excellent choice for rapid prototyping.
Another important benefit of additive manufacturing is its ability to decrease the number of defects in a final product. This is especially important for medical devices, which are often designed and produced to meet specific patient needs. For example, hearing aids can be made to a person’s exact specifications. This can help improve outcomes and ensure a comfortable fit.
3D printing is a relatively new technology that has been used in many industries, from aerospace to automotive to consumer electronics. The process has revolutionized the way companies produce products and can be a great asset for businesses. However, it is important to understand the risks of this technology, and how to avoid them.
Rapid prototyping
3D printing is a key tool in the product development process, allowing designers and engineers to quickly transform digital designs into physical prototypes. This allows companies to iterate more quickly and accurately, resulting in higher quality products that are more cost-effective. Using 3D printing for prototyping also reduces time to market and increases product reliability, which can help companies maintain a competitive advantage.
During the prototyping phase, designers can experiment with different materials, sizes, shapes, and colors to test how they will affect the fit and function of the product. This can save time and money, as well as reduce risk by avoiding costly mistakes. 3D printers also allow designers to create complex geometries and details that are difficult or impossible to make manually.
In addition, 3D printing can be used to create working prototypes, which are intended to demonstrate and validate the product’s functions. These prototypes are typically made in parallel to the industrial design phase, so that each function can be tested and refined before being integrated into a finished prototype. This helps to ensure that the product works as designed, and it can help to eliminate potential problems during the industrial design phase.
Another benefit of rapid prototyping is that it can help to improve communication between teams, which can increase productivity and speed up the product development process. This technology allows team members to share prototypes with others across the organization and get feedback from users and customers. It also makes it easier to gather data and support for product decisions, which can help to improve the final product.
Traditionally, product designers and engineers would create makeshift proof-of-concept models with basic tools. However, producing functional prototypes and production-quality parts requires expensive tooling and molds, making it impractical to produce them for short-term use or testing purposes. Moreover, these tools are often expensive and take weeks or months to make. 3D printing, on the other hand, can produce high-quality prototypes and end-use parts in a matter of hours. Furthermore, it can reduce costs by eliminating the need for costly tooling and molds, as well as reducing manufacturing overhead.
Mass-production
Production 3D printing is a relatively new industrial process that uses different materials to make products on an industrial scale. It allows manufacturers to produce parts that perform every bit as well as their CNC machined or injection molded counterparts, but at a much lower cost per unit. This allows for faster time to market and reduced capital expenditures.
In addition, production 3D printing allows for quick turnaround times to meet customer demands. This is particularly valuable in fast-moving industries such as automotive, aerospace, and medical. In some cases, manufacturers are completely switching to 3D-printed parts. For example, Canadian manufacturer Precision ADM used more than 100 Form 3B printers to produce Health Canada-approved nasopharyngeal test swabs that they sell to hospitals and doctors across the country.
Although 3D printing has been unable to compete with mass-production techniques like injection molding and CNC milling until recently, companies such as Adidas, Chanel, and Adidas Futurecraft have utilized it to produce a variety of products. This technology is also being incorporated into mass-production by other companies, such as medical device maker Formlabs. In addition to reducing production costs, mass-production 3D printing also offers flexibility in design. It allows for the creation of complex geometries that would be difficult or impossible to fabricate with traditional methods.
For instance, some companies have even used 3D-printed products to manufacture their own fabrics and other materials. This allows them to control the quality of their products and ensure that they comply with safety regulations. Mass-production 3D printing also reduces the amount of labor needed, allowing for greater productivity and efficiency.
As a result, manufacturers can quickly scale up and down their production without the risk of large investments in tooling or machinery. The ability to switch between various production processes can also be beneficial for a business that has a diverse product line, as it enables them to quickly meet customer demand.
The manufacturing industry is constantly changing, so it’s important to find the right production method that will work for your company. With the right printers and materials, you can improve your speed to market and create more innovative products.
Customization
Customization is a powerful tool that allows manufacturers to produce products that are unique to each customer. By enabling customization, companies can reduce production costs and improve their market competitiveness. In addition, customized products can improve user experience and increase customer satisfaction. Customization is also a great way to differentiate products from competitors and create a unique brand identity.
3D printing is a powerful technology for mass customization, as it eliminates the need for tools and molds and enables on-demand manufacturing. As a result, it can shorten lead times and lower production costs. The ability to print parts on demand also helps manufacturers reduce inventory and storage costs, which can save money in the long term.
To successfully implement mass-customization, it’s important to optimize designs for 3D printing. This involves incorporating features such as lattice structures and topology optimization for lightweighting and efficient material usage. These features can help businesses achieve their desired product design without sacrificing performance or quality.
SLA 3D printing can be used to make customizable consumer goods that reflect the needs and preferences of consumers. For example, it can be used to create personalized eyeglasses that fit the wearer’s facial shape and style. It can also be used to make customized medical devices, such as dental implants and prosthetics, which are tailored to each patient’s anatomy.
In addition to improving the functionality of a product, customized 3D prints can add visual appeal and brand recognition. These benefits can help companies improve their market competitiveness, especially in industries where competition is intense. Customization also makes a good marketing strategy for products in high-demand niches, such as sports equipment or automotive components.
Another advantage of 3D printing is that it can create complex geometric shapes that are difficult to machine or cast. This makes it an ideal production technique for manufacturing complex, functional parts. In addition, the process can be used to create a wide variety of materials, including metals and ceramics.
Despite these advantages, there are some challenges with mass-customization using 3D printing. Creating a new part requires extensive planning and design work. In addition, post-processing is required to finish the final product. This may include sanding and smoothing to achieve a specified finish, removing support struts, heat treatment for specific material properties, or final machining.